①当社製品をお届けするまで
みすまる産業では、フィルム原反を入荷した後、
印刷・ラミネート・スリット・製袋までの加工を一貫して
行えることが強みです。
最終製品は、印刷・ラミネートを行い、スリット加工をしたロールの状態か、
必要に応じて製袋加工をした状態で出荷されます。
事業フローチャートはご覧の通りで、製造部(製造第1課・第2課)を中心に、
他の部門・部署が様々な形で携わっていることがわかります。
営業本部によるお客さまからの受注の後、
業務部(事務担当)による生産指示(作業指示)と、
状況によっては新版/原材料/副資材の仕入を実施。
業務部(倉庫担当)による原材料等の準備フォローを受けて、
製造部による生産が開始。製造工程中、品質管理室が適度チェックを行い、
でき上がった製品は自社倉庫あるいは外注先倉庫で保管。
そして、製造部やお客さまとの調整で決まった納期に基づいて、
業務部(事務担当)の指示により、自社倉庫あるいは外注先倉庫より出荷。
この一連の入金/出金(当社からのお支払い)の流れについては、
売掛金/買掛金という形で、総務・経理部で管理されます。
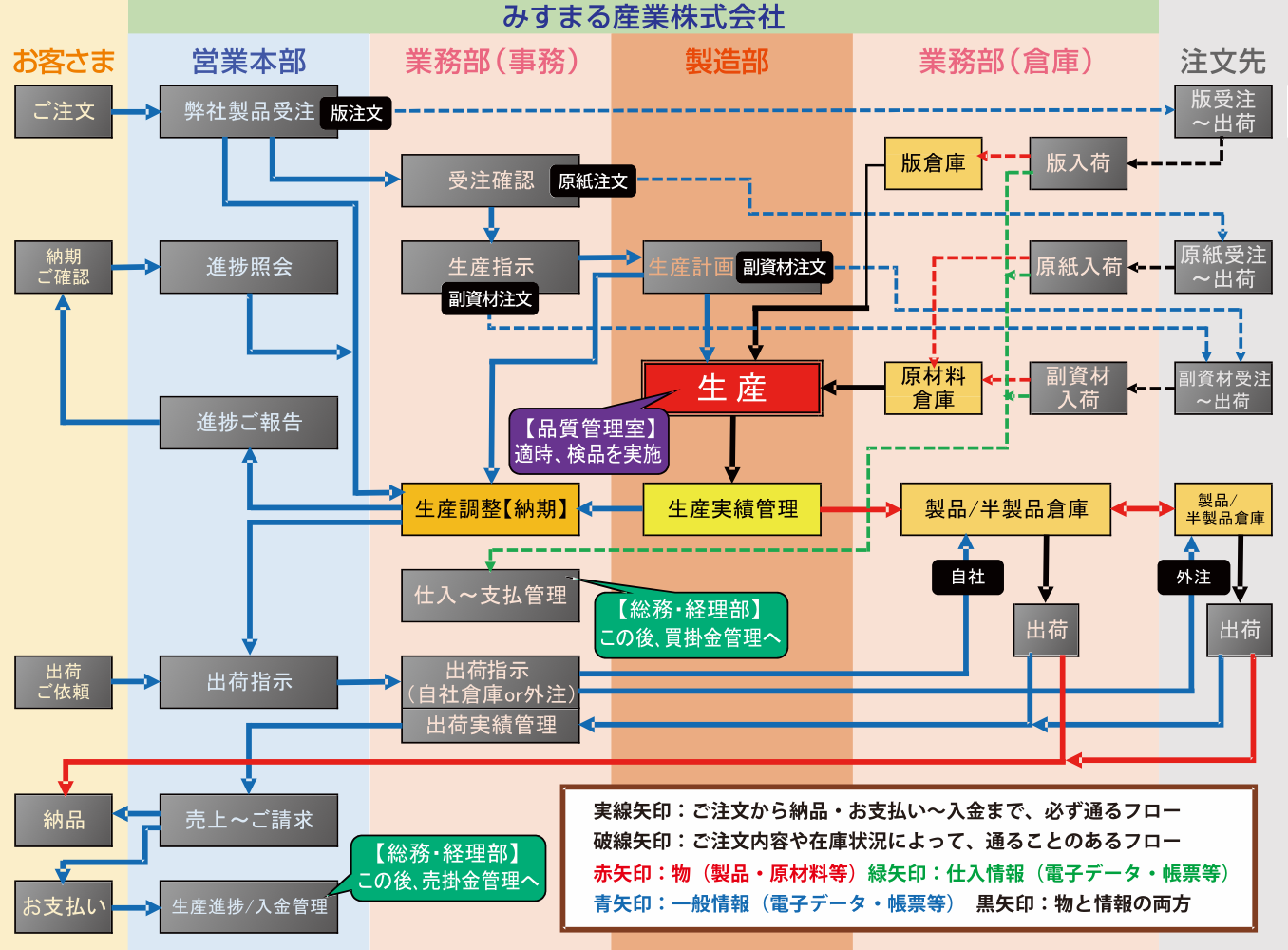
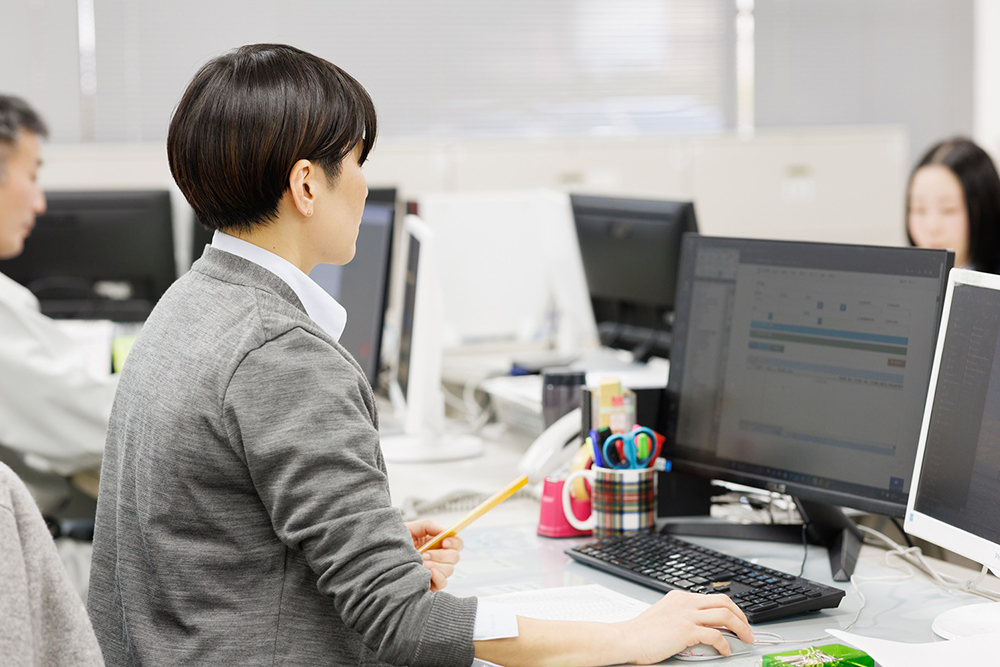
受注から出荷~納品と入出金までの一連のフローは全て、当社用にカスタマイズした基幹システムで一元管理されています。かつてはOffice系ソフトの帳票等で管理していましたが、情報の抜け・漏れ・入力ミスや認識の齟齬等が多く発生していたため、全社をあげて事業フローのシステム化を実施。
営業本部での受注や業務部(事務担当)の生産指示と進捗管理等のデータはPCで入力。受注は全てNo.管理されているので、生産の進捗確認や過去の生産実績を簡単に参照できます。そして、倉庫の原材料や副資材置き場には全ての収納棚に品目単位でQRコードが付けられており、業務部(倉庫担当)は対象物品の出し入れを行うたびに、所持しているハンディターミナルでQRコードを読み込み、在庫の数量を管理。
これにより、定期的に実施している当社の棚卸しも、わずか1時間程度で完結!
この基幹システムの導入で、当社は以前とは比較にならないほどの情報処理能力と生産性の向上、業務効率化を成し遂げることができました。
②製造工程
【各部門の紹介】のページでもご紹介の通り、当社製造本部は
「製造部(製造第1課・第2課)」「業務部(内、本社の事務担当においては、工程管理課/資材課/倉庫物流管理課)」の
2つの部署で構成され、実際に製造を行う部署は製造部になります。
製造第1課は印刷工程~ラミネート工程~エージングと、
有機溶剤を扱う機会の多い前段階の工程を担当し、対する製造第2課は有機溶剤を扱わない、
仕上げの工程(スリッター工程と製袋工程)を担当します。
これらのうち、どの工程を経て納品されるかは、お客さまからのご注文内容によります。
また、製品完成に向けて、必ずしも同一の工場で全ての工程が行われるとは限りません。
工程によっては当社の別工場に輸送した上で行うこともありますし、
当社の製造キャパシティの状況やご要望を実現するための加工方法によっては、
最後は「半製品」という形で外部の業者様に外注~仕上げていただくこともあります。
いずれにせよ、いかなるご注文にも早く、正確にお応えできるよう、
リアルタイムで工程管理を行っております。
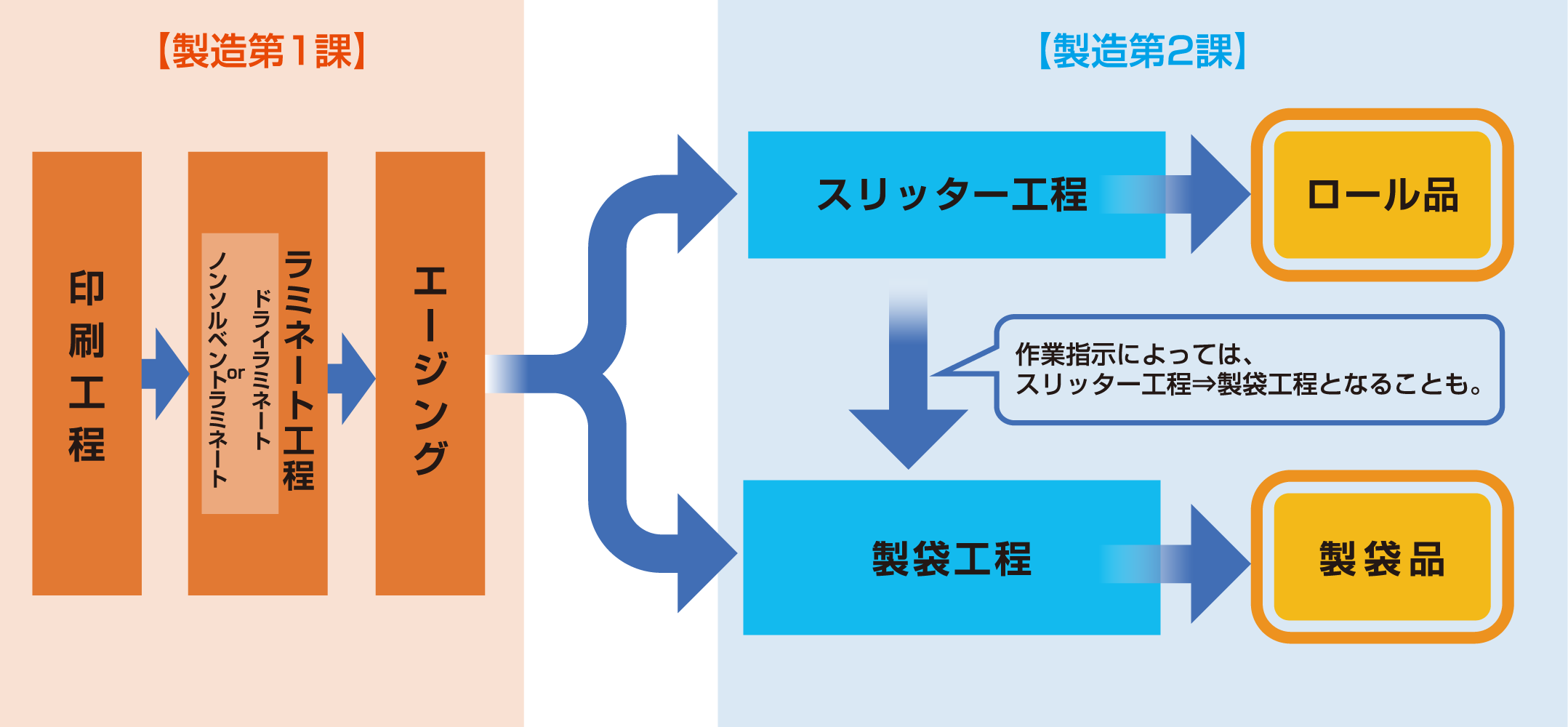
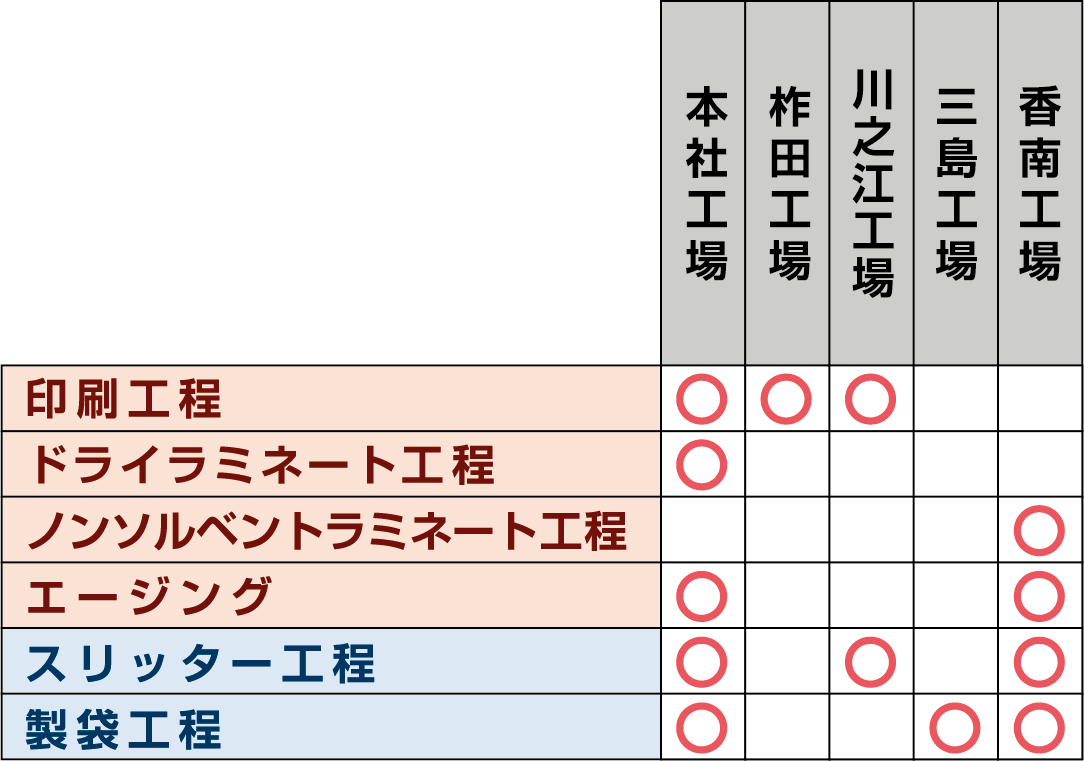
当社は、本社工場の他にも製造拠点を複数設置しており、その数は全部で5拠点。
この表は各工場においてどの工程に対応しているのか、一覧にしたものです。最初の工程である印刷工程、仕上げのスリッター工程と製袋工程は数の多さゆえ複数の工場で対応しており、仮にひとつの工場が天災等の理由で稼働不能になったとしても、他の工場でカバーすることで、当社全体での稼働停止を防ぐことが可能です。
(1)印刷工程
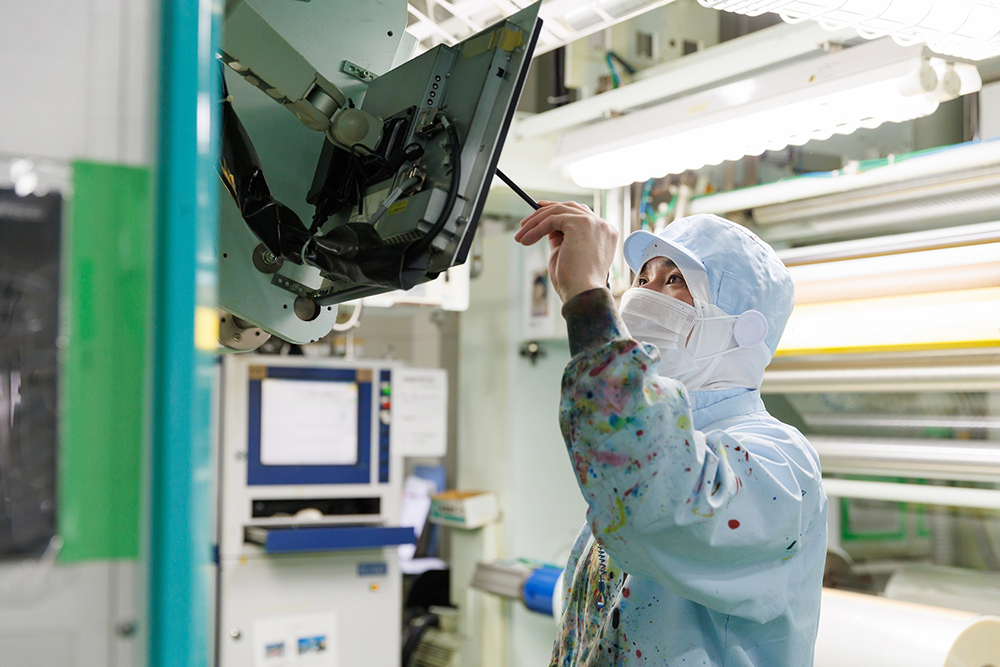
トップバッターの製造工程です。お客さまからご依頼のデザイン(お客さまからご指定のあるケースと、外部デザイナーを交えて調整・決定させていただくケースあり)に基づき、数本の版(鉄製シリンダー)を外注作成。用途に応じたフィルム(原反)と、当社内にて調色したインキにて印刷を行います。
まずはインキの調色からなのですが、三原色(C(シアン)、M(マゼンタ)、Y(イエロー))のみではご要望の色の表現が困難であるため、特色インキの使用や、あるいは色の硬度の調整を行うことで表現に勤しんでおります。
印刷は、1台の印刷機で複数のユニットを装備。1ユニットに1本の版をセットし、1色ずつ印刷~色を付けていく作業となります。当社では、所有している最大の印刷機で最高11色の印刷が可能ですが、印刷機の前方の7ユニットで7色印刷/後方の4ユニットで4色印刷といった、別々のご注文の振り分け印刷を行うことで、業務効率化をはかっております。
(2)ラミネート工程
ラミネート工程は、内容物の性質により、各機能を有したフィルムを貼り合せて多層複合化フィルムにすることにより、その内容物を外敵要素から保護することが目的です。
印刷工程で印刷を施したフィルム単体ですと軟包装資材としての必要強度を満たさなかったり、印刷面が直接中身に触れることになり、状態によっては最悪、触れたものがインキで汚れるおそれがあります。
ラミネート加工を行えば、そうしたことを防げる上、各々異なる性能(高温につよい「耐熱性」であったり、中身の香りを保ちやすい「保香性」、湿気を通しにくい「防湿性」等、様々な性能があります。詳しくはこちら)を持ったフィルムを貼り合わせることで、より高性能な軟包装資材として仕上げることが可能となるのです。
シンプルでわかりやすいように見えて、奥の深いラミネート加工。その加工方法には表の通り、2つの選択肢(ドライラミネート/ノンソルベントラミネート)があります。
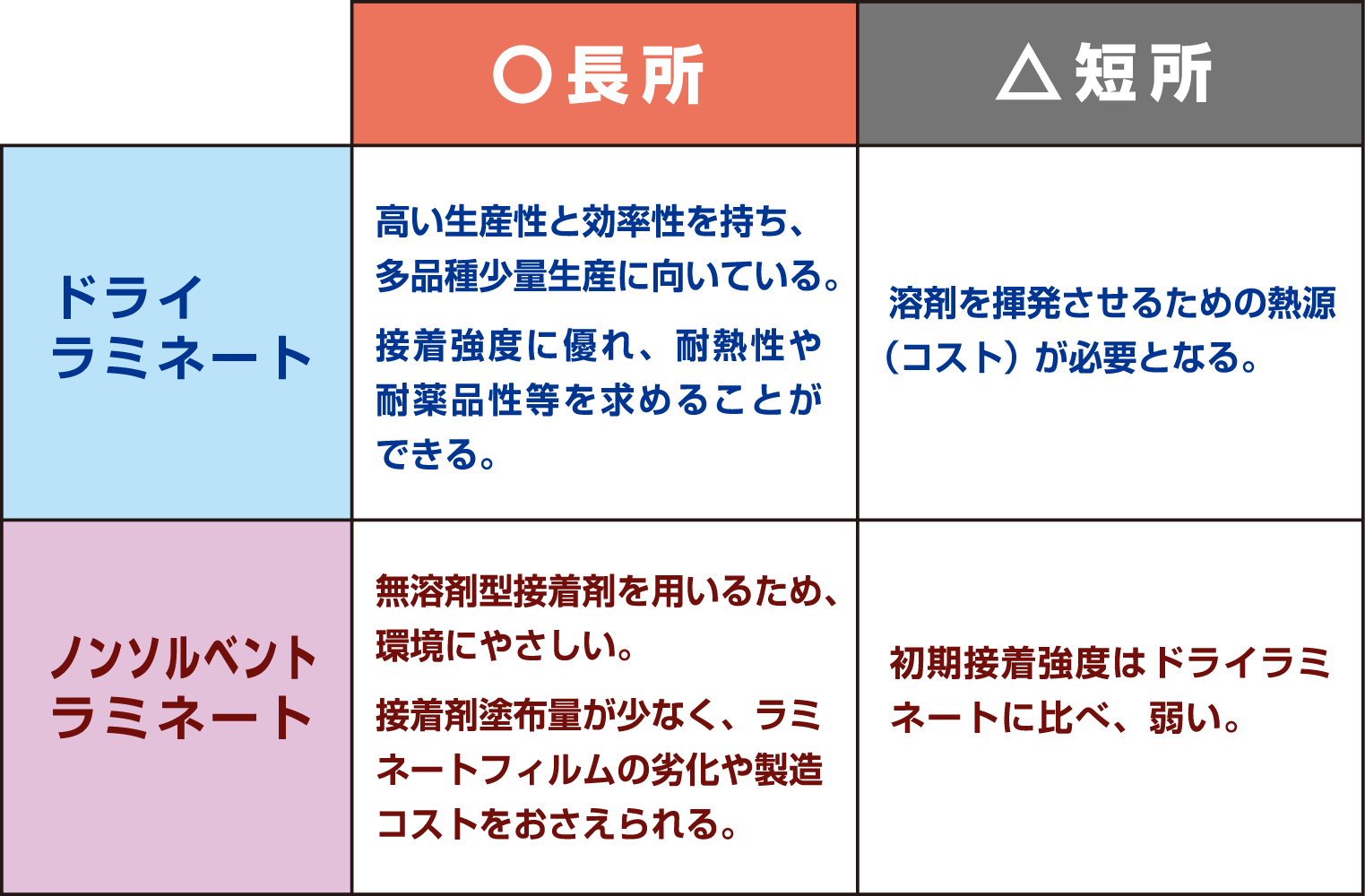
それぞれ長所と短所があり、お客さまからのご注文内容によって、加工方法を使い分けます。
一般的にドライラミネートは医療用包材やレトルト食品等の包材のような耐熱性や耐薬品性が求められる包材で、ノンソルベントラミネートはスナック菓子や日配食品の包材等、様々な用途で利用されております。
なお、当社では、ドライラミネートは本社工場で、ノンソルベントラミネートは香南工場で対応しております。
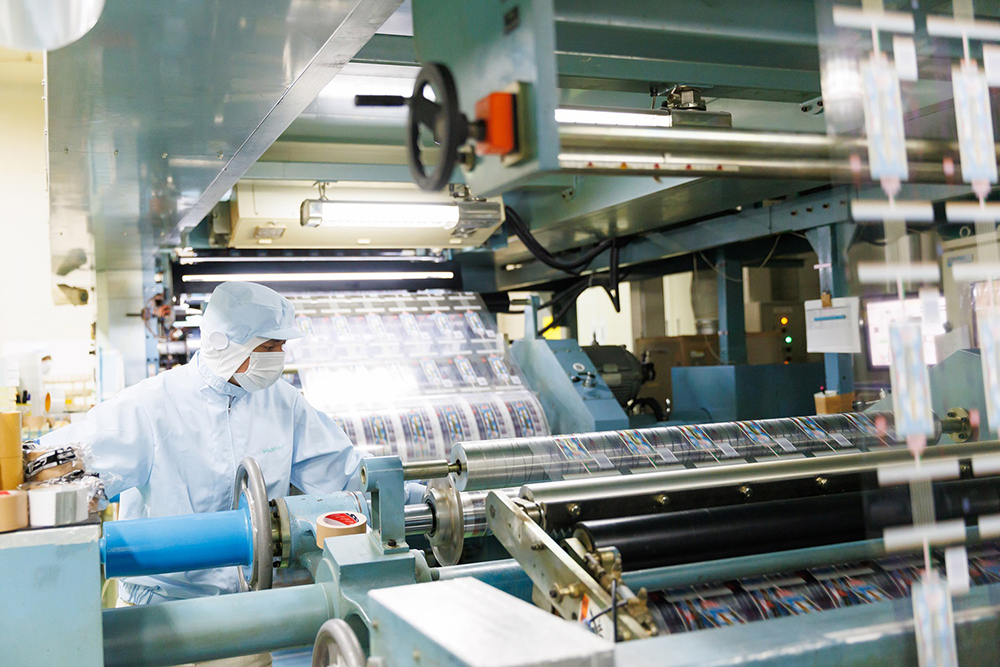
ドライラミネートは、接着剤を有機溶剤で希釈したものを、印刷したフィルムに塗布し、ドライヤーユニットで乾燥させて溶剤を蒸発させることで、別のフィルムと熱圧着させる加工方法です。
この加工方法で重要になってくるのが、接着剤の選定(主に、下記の2種類に大別)と希釈です。耐熱性や耐薬品性等、包材の用途や塗布~貼り合わせるフィルム同士の性質も考慮して、選定と粘度調整を行わなければなりません。
-
*エーテル接着剤
【長所】
低コスト、エージング時間も短くて済む。
【短所】耐熱性・耐内容物性に劣る。
-
*エステル接着剤
【長所】
耐熱性・耐内容物性に優れている。
【短所】コストが高く、エージング時間も長い。
なお、ラミネート後は接着剤を硬化させるため、適正に温度管理されたエージング室で熟成させることになります。
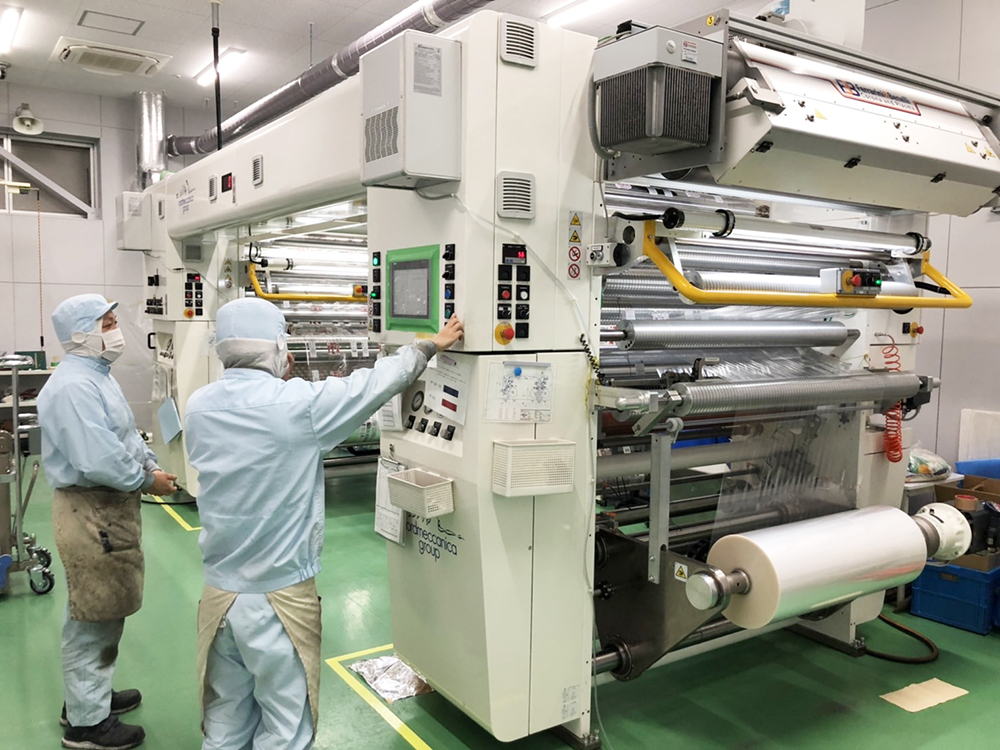
ノンソルベントラミネートは、無溶剤型接着剤を利用したラミネート工程です。有機溶剤を使用しないので、環境にやさしく、ドライラミネートと違いドライヤーユニットでの乾燥も不要。接着剤塗布量が少ない分、製品の軽量化と接着剤の節約による低コスト化も望めます。
いいことづくめのように見える加工方法ですが、最大の課題が初期接着強度の弱さ。トンネリング(フィルム上の接着面と別のフィルムとの間に浮き・剥がれが、巻取幅方向に筋状に発生する現象)が起きやすく、品質管理の難易度はドライラミネートより上であると言えます。しかしながらメリットが多いことも事実であり、ドライラミネートとの場合に応じた使い分けで対応致します。
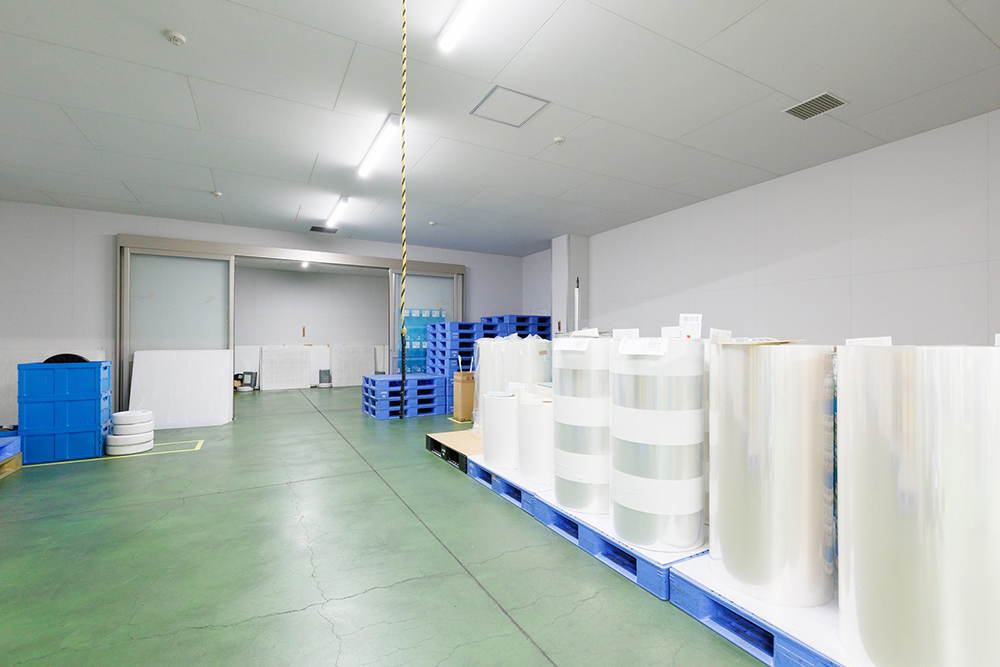
エージングとは、ラミネート加工で貼り合わせたフィルムを、適正に温度管理された部屋で一定期間保管し、フィルムの接着剤を硬化させ、安定させることです。温度と時間の管理が肝要であり、接着剤の硬化速度は接着剤の種類や季節ごとのフィルムの温度によっても変動します。
使用している接着剤には、それぞれメーカー様からいただいた詳細資料があり、その情報を基にエージングの温度と所要時間を決定します。温度は40度前後、所要時間は1日から最長で7日と、多種多様です。
(3)スリッター工程
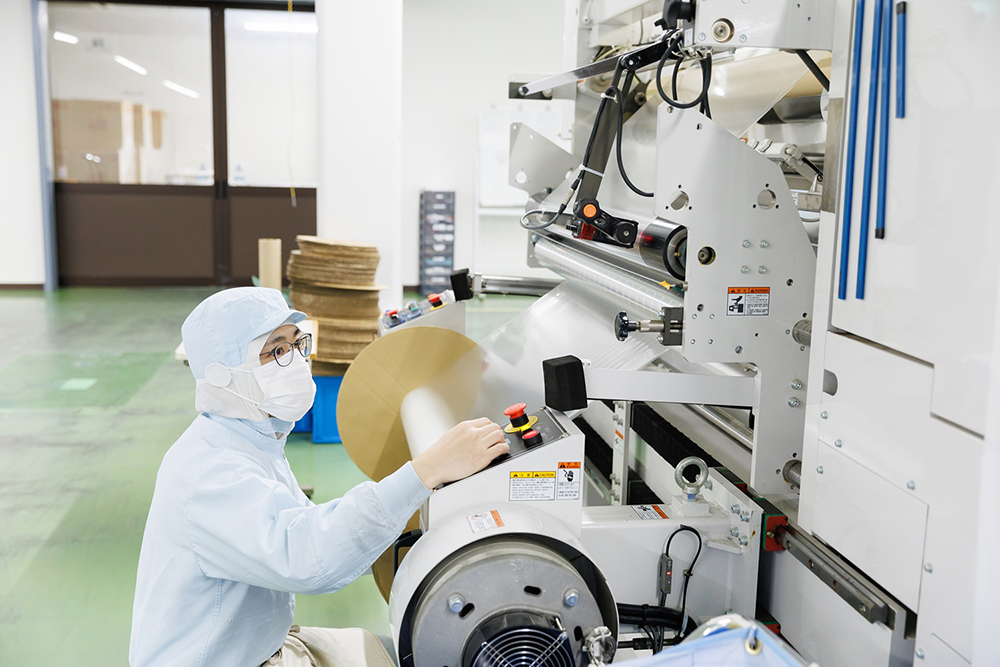
お客さまからのご注文に合わせて、エージングを終えたフィルム(原反)で不要な部分の切断(スリット)を行い、ロール状に巻き取って仕上げる工程です。「スリッター機」と呼ばれる、切断と巻き取りの両方を行うロール加工機械を用いて行われます。
この工程では、スリッターの切断条件と巻出・巻取での張力(テンション)バランスが何よりも重要で、各種材料の特性に合わせた切断方式と張力制御の設定・調整力が求められます。
また、前工程(印刷、ドライラミネート)からの不具合箇所の発見・除去についても、スリッター工程での対応が要となります。前工程からのラベルや画像での情報を元に、スリッター工程で目視確認にて除去、継ぎ直し等の処置を行います。
さらに、巻き替え検査機による検品や、状況に応じて巻き直しも行い、多様化するお客さまからのニーズにお応えしております。
(4)製袋工程
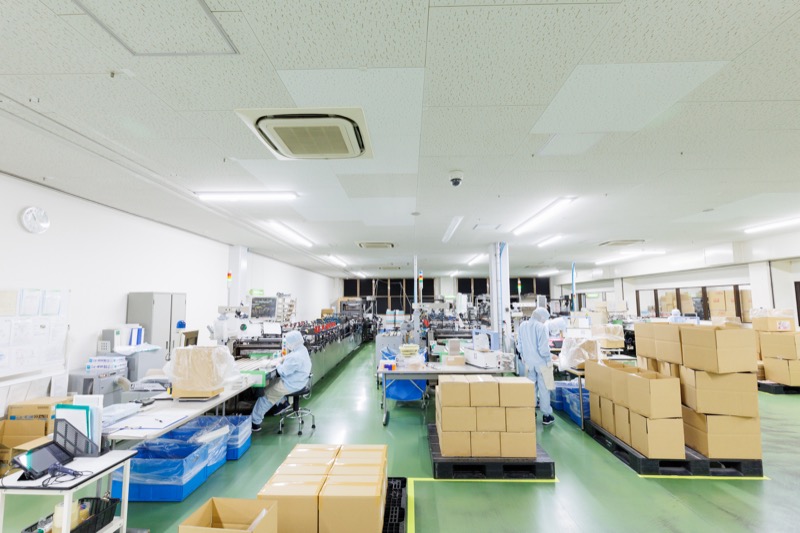
当社の製造工程の最終段階となるケースも多い、フィルム(原反)を袋状に加工し、シール袋を製造する工程です。フィルム(原反)の外面より熱を当て、外面は溶けずに内面が溶ける様、温度を調整し貼り合わせ、冷却~ピッチごとにカットして、一枚のシール袋となります。
接着(シール)をフィルム(原反)のどの部分で行うかによって、三方袋、合掌袋、スタンドパウチ等、様々な形態のシール袋に加工。お客さまがお使いになる目的、封入予定の中身によってどの形態の袋が適しているか決まりますので、営業本部との連携でご提案も行います。
製袋機は大掛かりなものが多く、1台あたり2名で動かしますが、一般的なライン製造作業とは異なり自身の裁量で作業を進められますので、負荷も小さく、入っていただけやすい環境です。
(5)製袋工程(サイドシール加工)
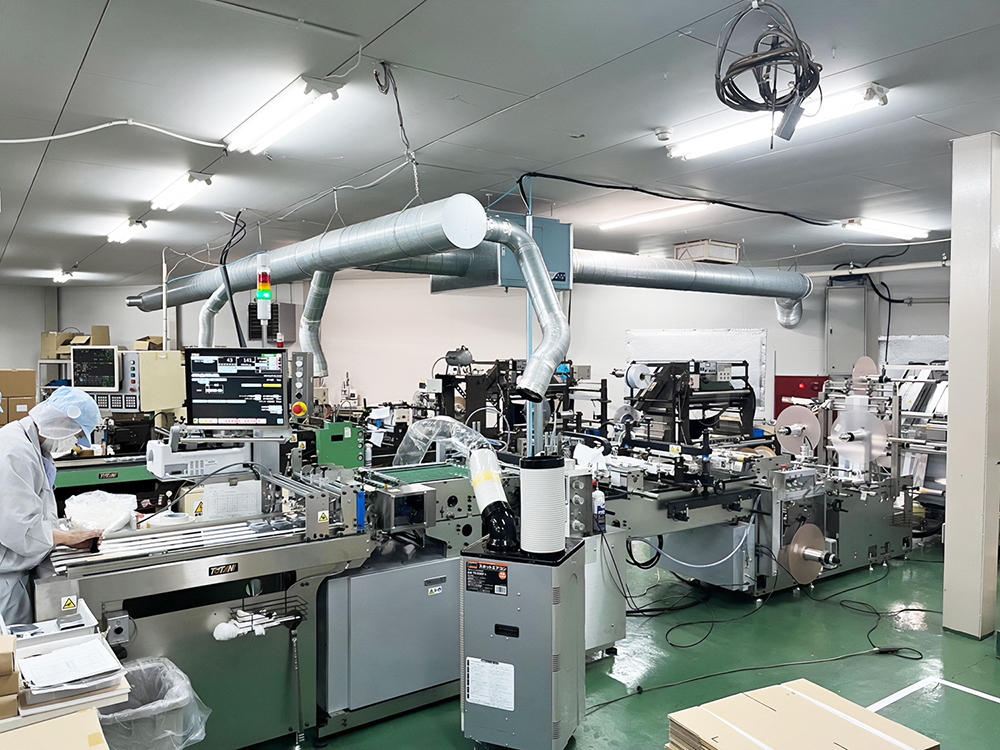
サイドシール加工とは、フィルム(原反)を折り、両端2か所の側面(サイド)を熱刃で溶かして切断し、同時に接着(シール)させることで行う製袋加工方法であり、別名で「溶断」とも呼称されます。
通常のシール袋と違い、周囲に「耳」のない袋を製造。仕上がりの見た目も美しく丈夫ですが、最大の特徴は、大きくて長いサイドシール加工機のフィルム通過道中で、フィルムの折り方を変えたり、様々な装置を組み合わせることで、色々な形状の袋に変形加工させることが可能である点です。
そのバリエーションはまさに多彩。変幻自在な当社の加工技術にはお客さまからも様々なご要望をいただいており、実際に完成させた製品のでき栄えには驚愕のお言葉をいただくことも。
いつ、いかなる条件でもお応えできるよう、空き時間を見つけては試作を行い、変形加工の可能性を追及しております。
(Ex)品質管理/品質保証
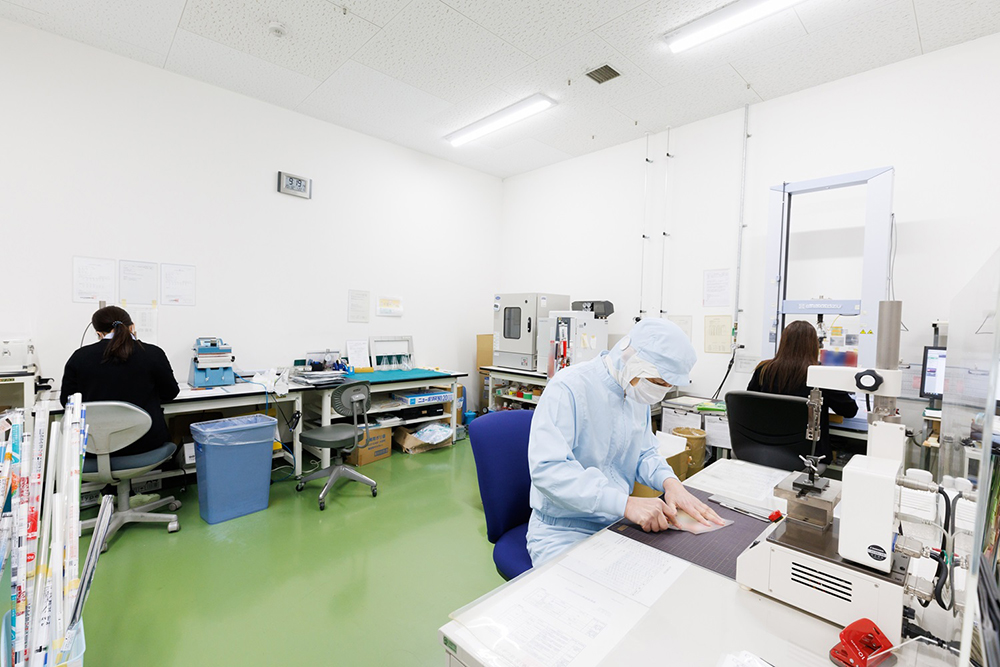
上記の製造工程において、製品の品質が高い水準で維持されているかどうかの確認と、そしてより良いものづくりを行うための改良・改善の推進役が品質管理室です。
工程のところどころでチェックを課することで、厳しい品質管理体制を構築。例えば、印刷工程後でお客さまのご要望通りの色の表現ができているかの確認を行ったり、製袋工程において採取したサンプルに対し、引張強度試験や耐圧試験、水漏検査等を行い、内容物を確実に守れるかどうかの耐性をチェック。
定められた安全基準値をクリアしているかどうか、しっかり見極めます。不具合発生のご連絡のあった際は、製造部の現場に赴いての状況調査と対策の立案、そして製造本部内で共有を行い、対策実行の支援まで行います。
過去の事案はすべて記録を残しており、トレーサビリティとしての備えも万全。このノウハウを有効活用し、不具合が発生してからの対処より、不具合そのものを未然に防ぐための支援を行っていけるようになることが目標です。
③環境保全の取り組み
みすまる産業は、地球環境にやさしく、社員とそのご家族の生活を守り、
お客さまや地域の皆さまから信頼される企業であるべく、
事業活動を通して各種課題解決に取り組んでおります。
その取り組みは、下図の4つに分類されます。「働き方改革」に伴い、
社員が日々楽しく働けるように人事制度を変革する「社内環境の整備」、地元の方はもちろん、
外部から興味を持ってこられた方も積極採用する等して
地元の魅力を発信するお手伝いを行う「地域社会への貢献」、
仮に災害や事故等が発生しても、高品質な製品を途切れることなく提供する「安全・安心な製品提供」、
工場内のハード面の各種取り組み「環境保全」で構成。
内、「環境保全」については、画像でより詳しくご紹介しましょう。
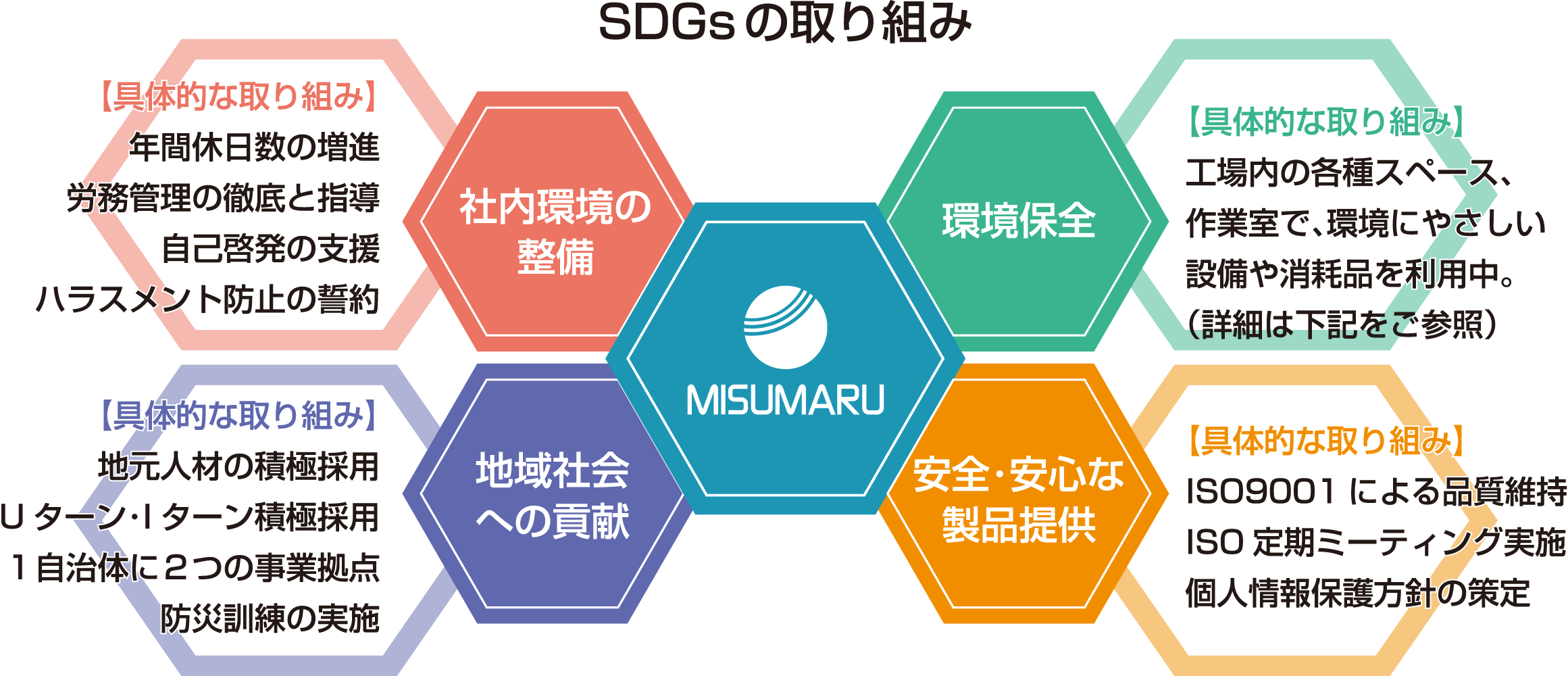
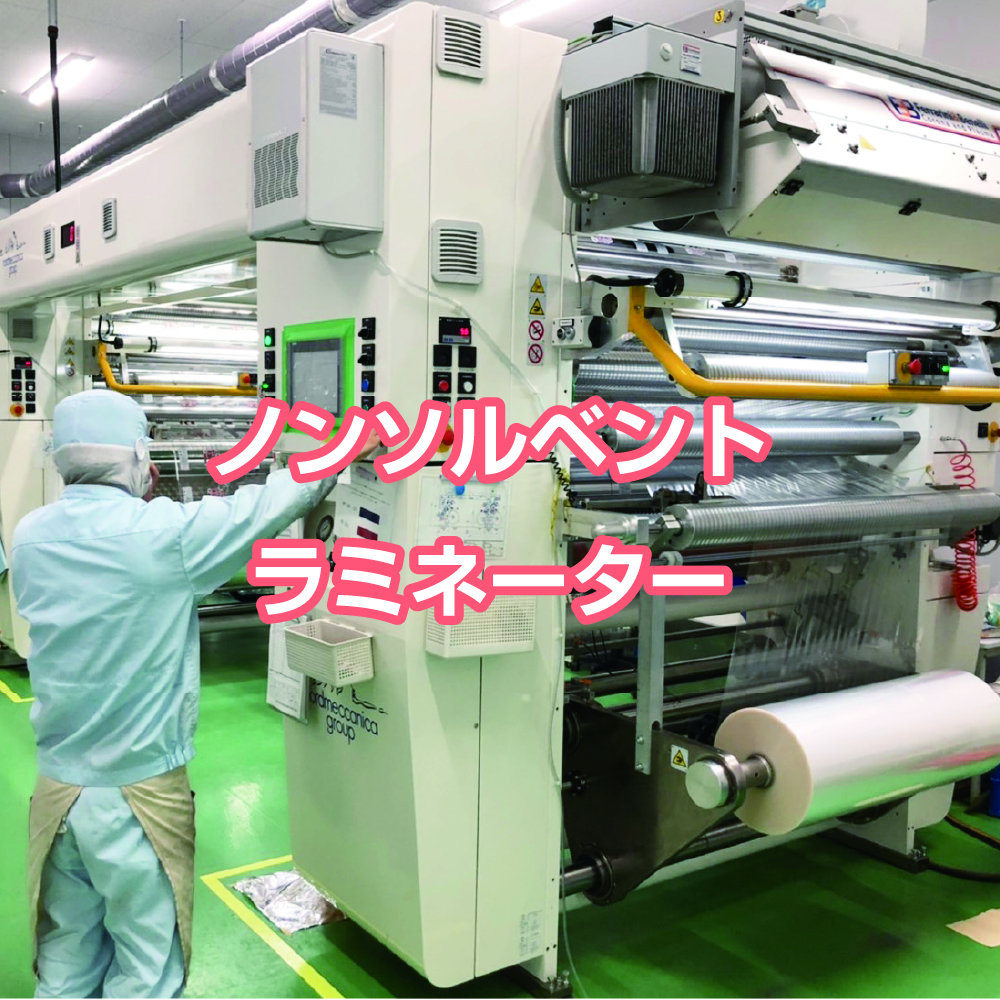
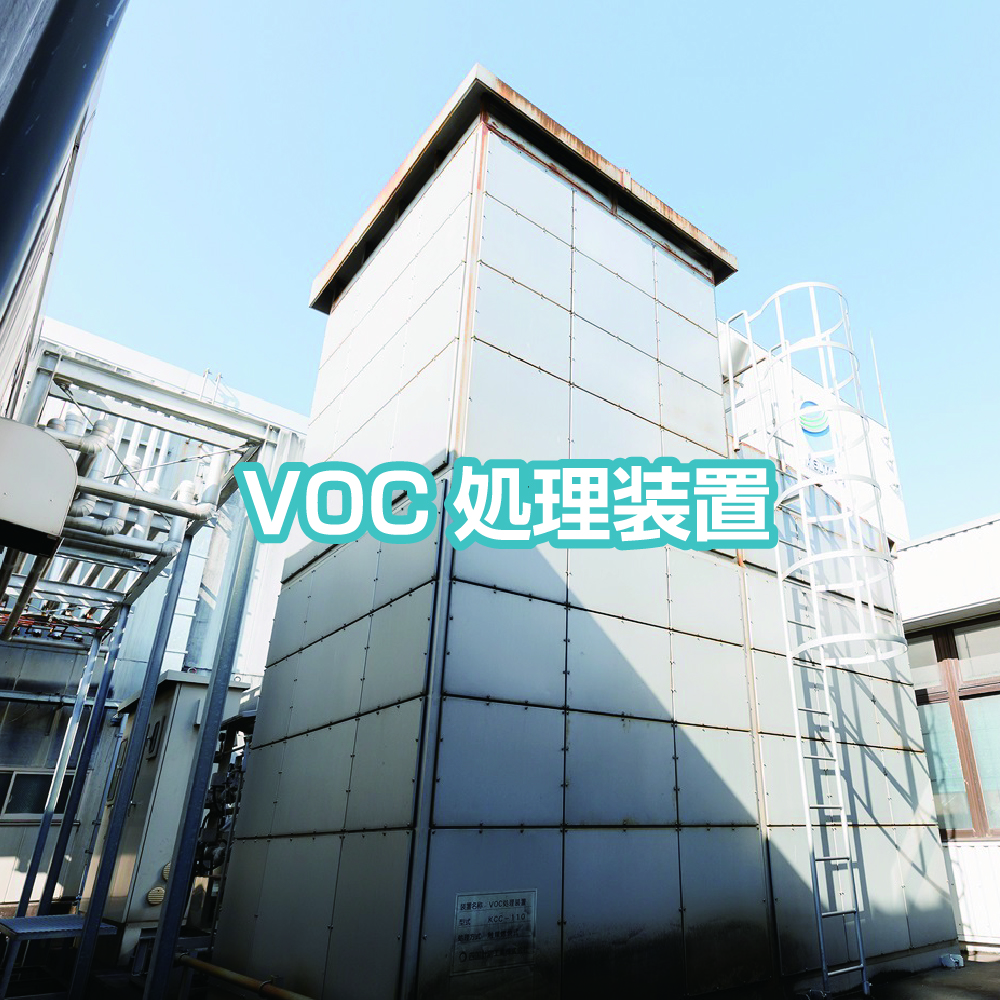
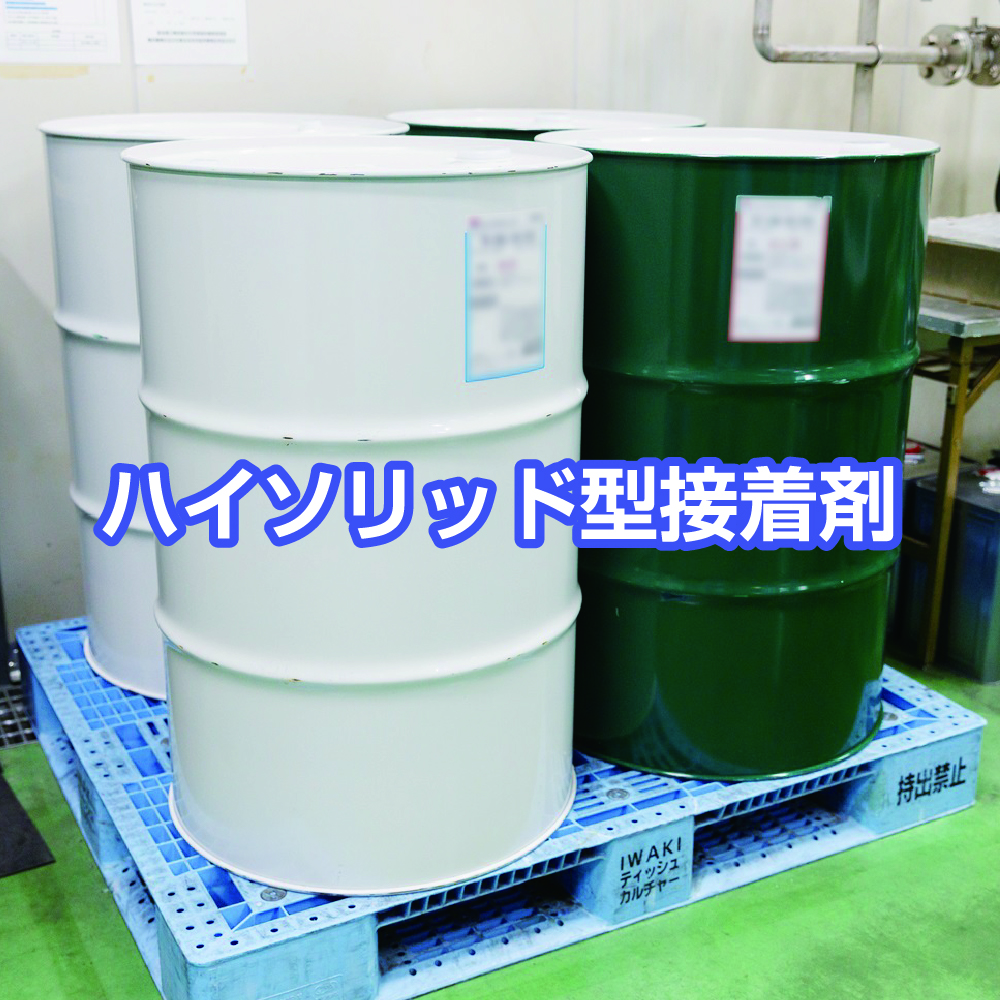
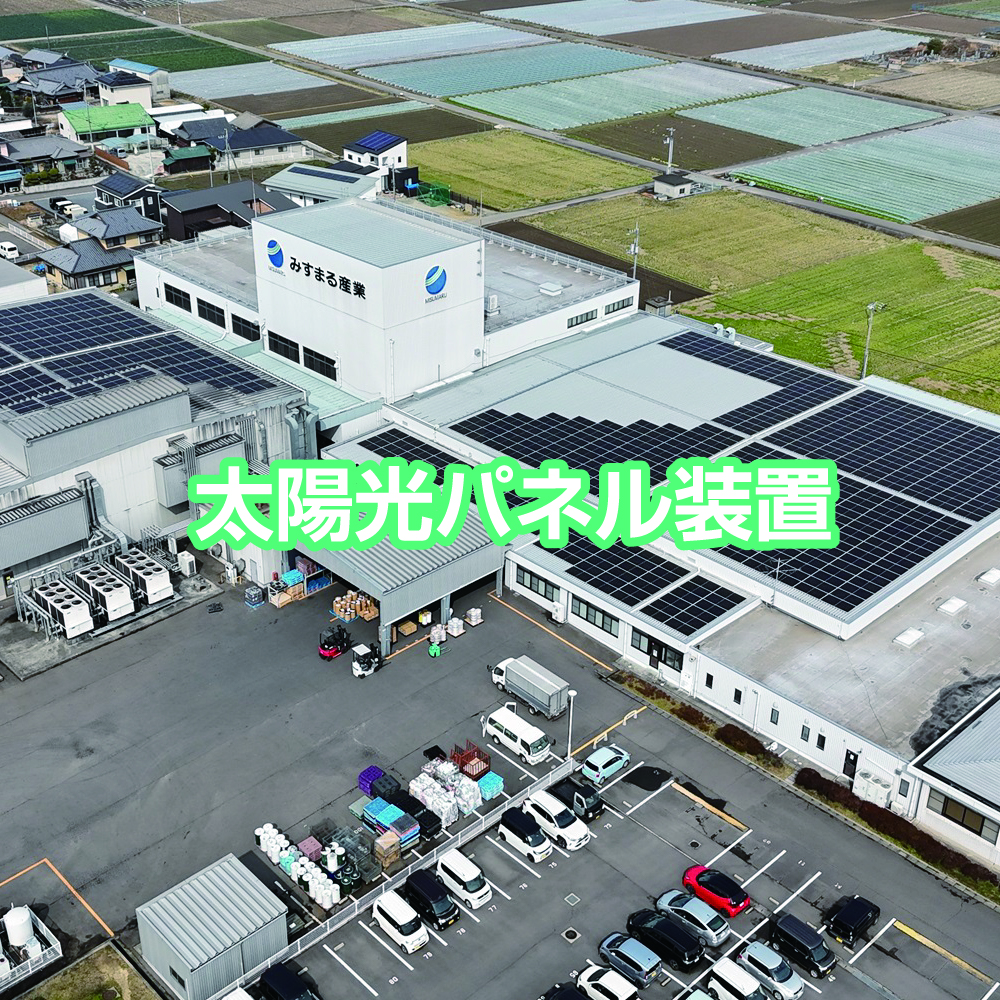
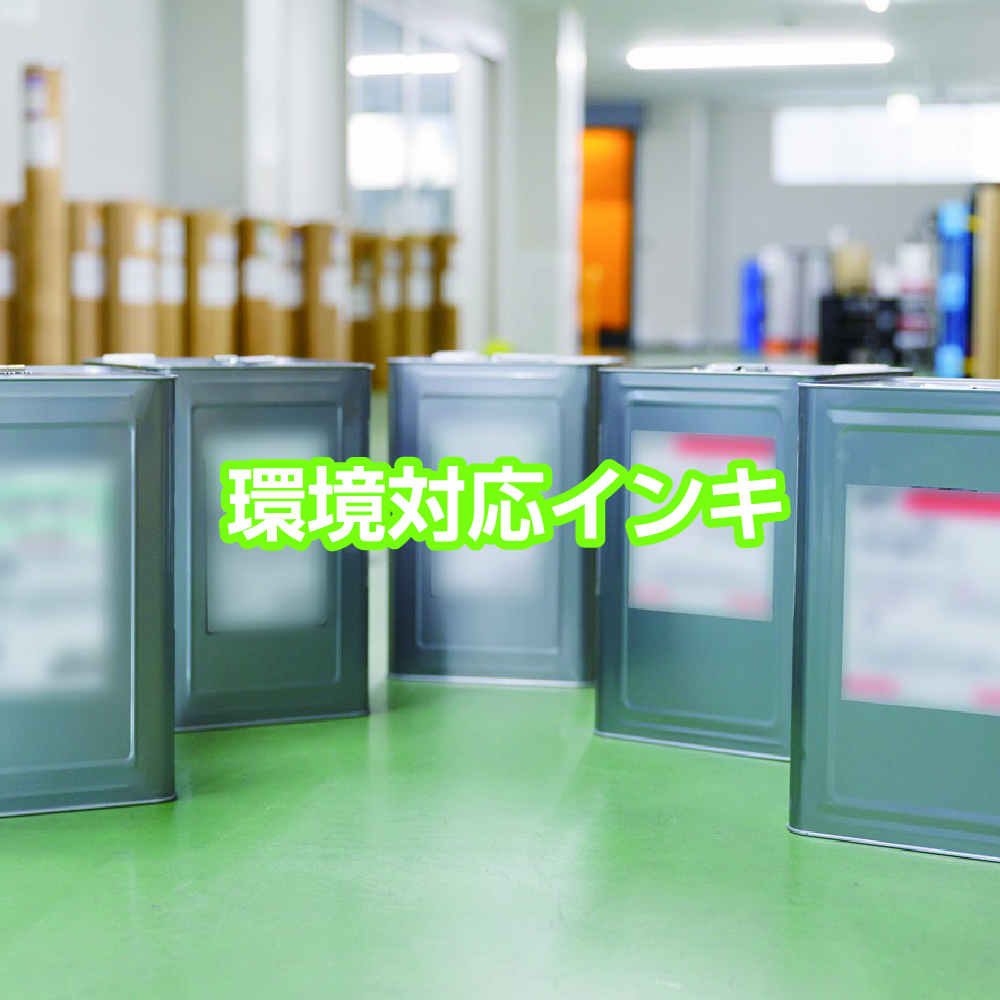
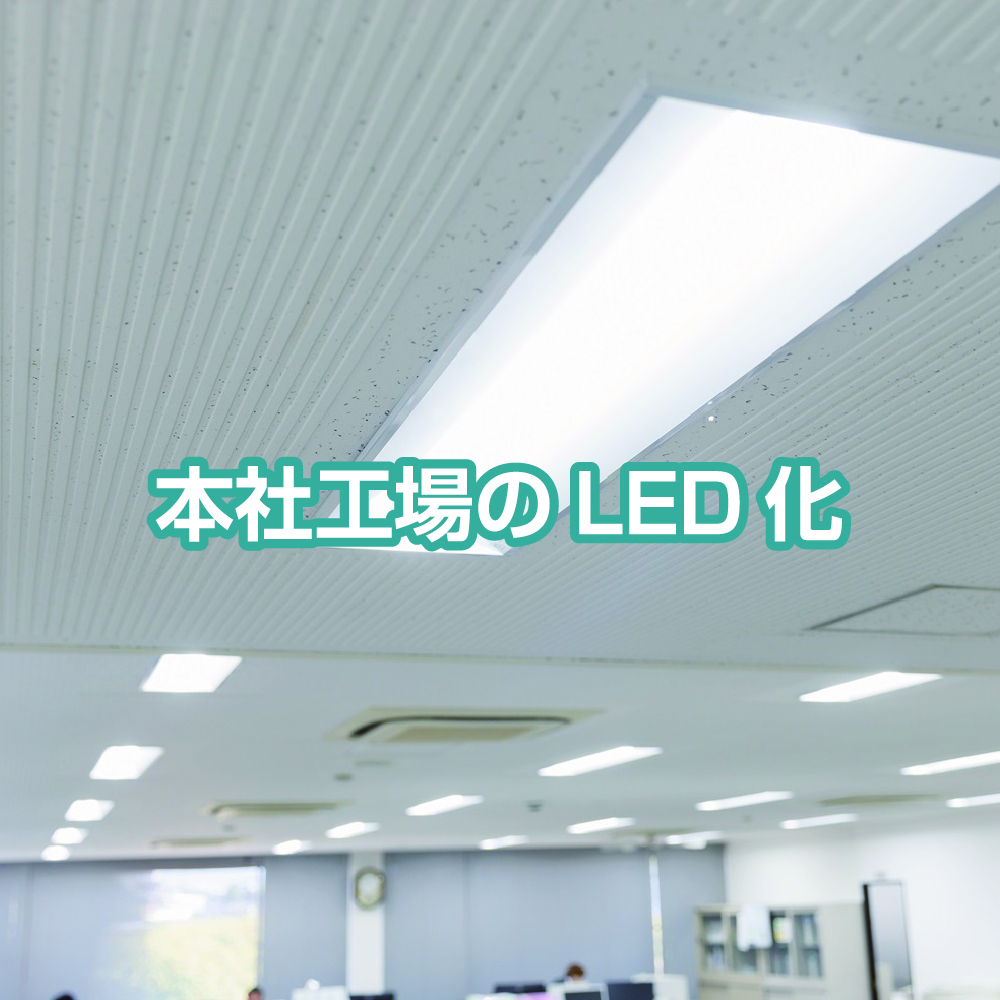
ノンソルベントラミネーター
ノンソルベントラミネート加工を行う、ラミネート加工機です。
先述の通り、有機溶剤を使わない加工方法なので、VOCガスが排出されず、地球温暖化の原因となるCo2ガスの排出量の削減が可能となります。
初期接着強度という課題はありますが、無公害かつ高品質な加工方法で、一石二鳥です。
VOC処理装置
VOCとは、Volatile Organic Compoundsの略で、揮発性有機化合物(有機溶剤等に含まれる有機化合物という化学物質の総称)のことです。
VOCは蒸発しやすく、大気汚染の原因となるため、製造工程で用いた有機溶剤は廃棄の際、適切に処分しなければなりません。
これは、工場から排出されたVOCを捕捉・除去し、クリーンなガスを大気中に排出するための装置です。
ハイソリッド型接着剤
固形分が多く、有機溶剤の使用量が少ない、ニュータイプの接着剤です。
ドライラミネート加工で使われますが、有機溶剤使用量の少なさゆえにCo2ガスの排出量も削減可能で、環境負荷の低減が期待できます。
太陽光パネル装置
本社工場の社屋に太陽光パネルを設置し、太陽光による自家発電を実施。発電では地球温暖化の原因となるCo2ガスを排出しないため、地球環境保護と脱炭素に貢献できます。
なお、発電した電気は当社本社工場の設備や装置、機器の稼働のために使用。省エネの一環としての取り組みでもあります。
環境対応インキ
植物由来の資源を原料の一部に使用して製造したインキを「バイオマスインキ」といいます。 バイオマスインキは、原料の植物が成長する過程でCo2を吸収するため、廃棄の際に燃焼したとしても全体としては地球温暖化の原因となるCo2量が増加しない「カーボンニュートラル」の考え方に基づいています。
本社工場のLED化
従来の既存照明機器からLED照明に変えることで、当社本社工場の消費電力(とそれに比例して電気料金)を大幅に削減。安全で明るく、目にも優しいので、省エネと同時に職場環境の整備もかないました。
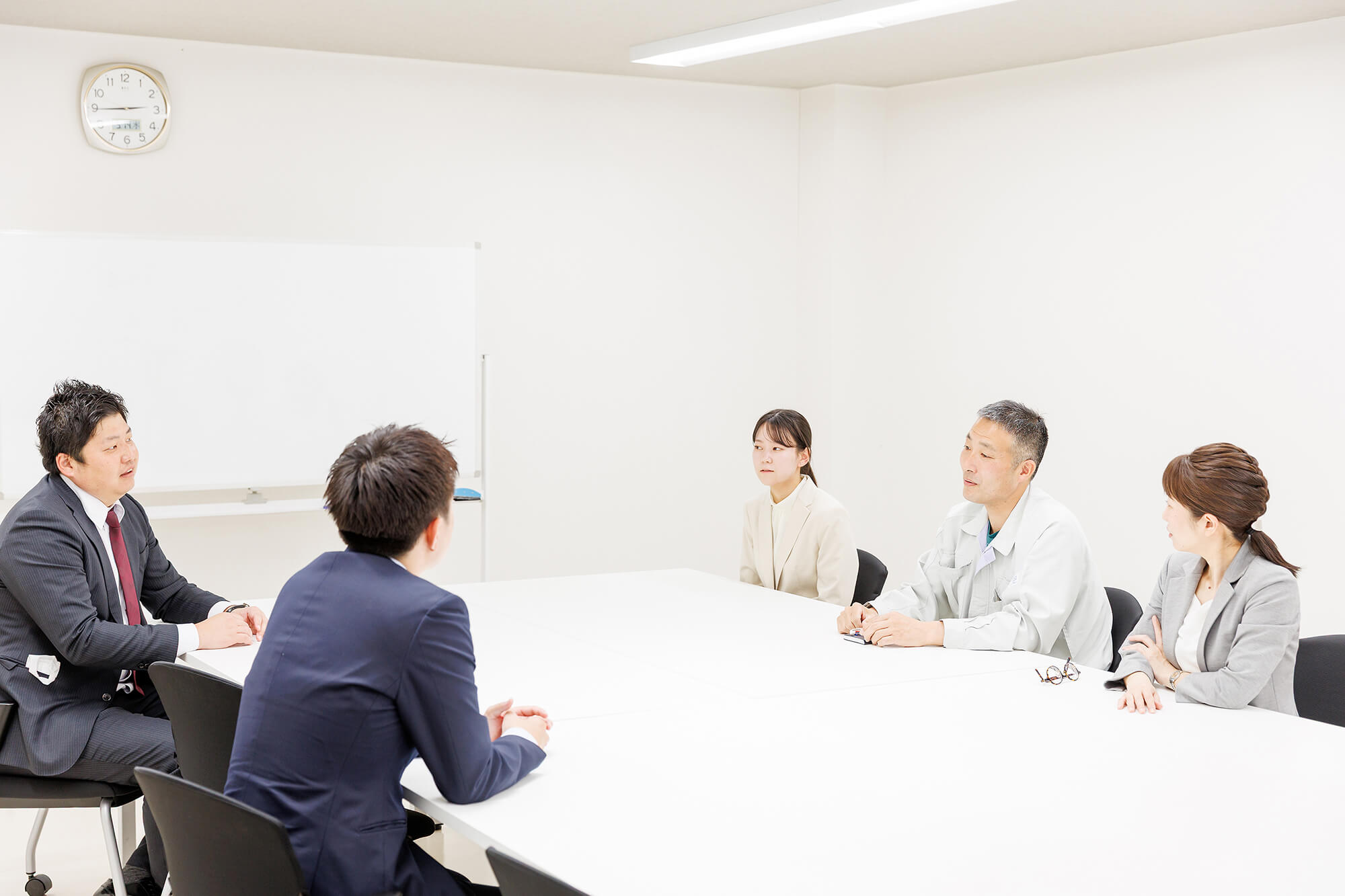